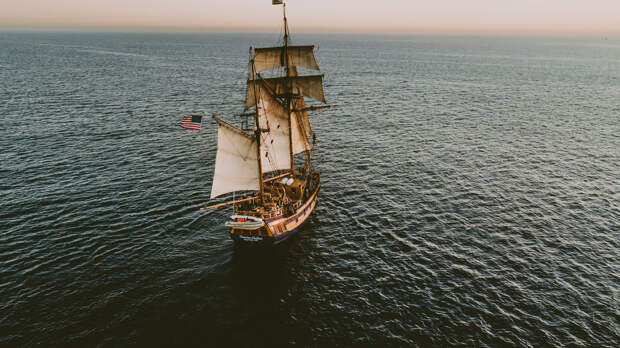
In deepwater operations, inspecting and maintaining subsea infrastructure is no easy task. The deep ocean is a challenging and often hazardous environment, with extreme pressures, low temperatures, and poor visibility. Yet, these factors don’t stop industries such as oil and gas, marine research, and environmental monitoring from requiring consistent and precise inspection of underwater assets. Remotely Operated Vehicles (ROVs) have emerged as powerful tools for visual inspection, enabling workers to safely examine, assess, and repair subsea infrastructure from the surface. ROVs equipped with high-definition cameras and advanced visual systems are revolutionizing deepwater inspections, providing clearer, more detailed views of underwater structures than ever before.
In this article, we explore how ROVs are enhancing visual inspection capabilities in deepwater operations and reshaping the future of subsea infrastructure management.
The Role of Visual Inspections in Deepwater Operations
Visual inspection is one of the most vital methods for assessing the condition of underwater infrastructure. In deepwater operations, subsea structures such as oil rigs, pipelines, cables, and marine renewable energy systems are subject to the stresses of the ocean environment. Over time, corrosion, physical damage, and other issues can develop, making routine inspections critical for preventing equipment failures and costly repairs.
However, conducting visual inspections at depths of hundreds or even thousands of meters below sea level presents several significant challenges:
- Extreme Depths: Traditional human divers can only operate within certain depth limits due to the risks posed by high pressures, cold temperatures, and decompression requirements.
- Hazardous Conditions: Strong currents, low visibility, and the risk of encountering hazardous substances (e.g., oil leaks or gas plumes) make underwater environments unsafe for humans.
- Limited Access: Some subsea structures are located in hard-to-reach areas, such as deep trenches or remote parts of the ocean floor, making it difficult to perform thorough inspections using traditional methods.
ROVs are helping to overcome these challenges by providing high-resolution visual inspection tools capable of operating at great depths and in hazardous conditions. By sending real-time video feeds to operators on the surface, ROVs allow for comprehensive visual assessments without putting human workers at risk.
ROVs: The Robotic Eyes of the Deep
Equipped with a range of visual inspection technologies, ROVs are able to deliver crystal-clear imagery and highly detailed data, significantly improving the quality and accuracy of underwater inspections. These robotic eyes allow operators to inspect structures with unprecedented precision, even in the harshest of underwater environments.
1. High-Definition and 4K Cameras
The development of high-definition (HD) and 4K cameras has transformed the quality of visual inspections in deepwater operations. These cameras provide incredibly detailed imagery that allows operators to identify even the smallest cracks, corrosion spots, or signs of wear on subsea equipment. HD and 4K cameras capture sharp, vibrant images in real-time, enabling operators to zoom in on specific areas of interest and conduct thorough inspections.
- Increased Detail: With high-resolution cameras, operators can detect problems that may otherwise go unnoticed, reducing the likelihood of undetected damage escalating into a more significant issue.
- Real-Time Decision Making: Live video feeds from ROVs enable engineers and technicians to make immediate decisions on whether repairs or maintenance are needed, minimizing downtime and preventing further deterioration of subsea assets.
2. Multispectral Imaging
ROVs are also equipped with multispectral imaging systems that go beyond traditional visual inspection capabilities. These imaging technologies allow operators to see different aspects of an underwater structure that might not be visible to the naked eye. By capturing data across multiple wavelengths of light, including infrared, ultraviolet, and visible light, multispectral systems enhance the ability to identify damage or issues caused by factors like corrosion or biofouling (the accumulation of marine organisms on surfaces).
- Corrosion Detection: For example, infrared imaging can detect temperature changes in the structure’s surface, indicating areas where corrosion has occurred. This allows operators to focus their inspection efforts on these high-risk areas, ensuring that potential issues are addressed before they result in failures.
- Enhanced Visibility: Multispectral imaging also provides improved visibility in murky or low-light conditions, which are common in deepwater environments. This technology can differentiate between organic growth, rust, and other substances that might obscure important details in a standard visual inspection.
3. Sonar Systems and Acoustic Imaging
In addition to visual systems, ROVs are often equipped with sonar and acoustic imaging systems that provide operators with a view of the underwater environment even when visibility is poor. Side-scan sonar and synthetic aperture sonar (SAS) are commonly used to map the seabed and inspect subsea structures.
- Side-Scan Sonar: This technology creates detailed images of the seafloor and subsea structures by emitting sound waves and measuring the time it takes for them to return. Side-scan sonar provides a comprehensive “picture” of the underwater terrain, helping operators locate potential hazards, identify damage to infrastructure, and measure distances between structures.
- Acoustic Imaging: Acoustic imaging systems help generate 3D visualizations of subsea assets by utilizing sound waves to create detailed maps of structures and surrounding environments. This can be invaluable when inspecting complex or obscured equipment, such as pipeline joints or the underside of offshore platforms.
4. Robotic Arms for Close-Up Inspections
ROVs are also equipped with robotic arms that allow for precise manipulation of tools and the ability to interact with the underwater environment. These arms can be used to capture close-up footage of underwater structures or perform small-scale repairs. With the help of high-definition cameras, operators can control these robotic arms to conduct highly focused inspections of critical components.
- Camera-Mounted Arms: Some ROVs feature camera-mounted arms, which enable the camera to get closer to the target object while still maintaining optimal focus. This allows for clearer, more detailed visuals of hard-to-reach parts of subsea equipment.
- Tool Integration: In addition to cameras, robotic arms can be fitted with various tools such as suction devices, cutters, or mechanical grippers, allowing ROVs to not only inspect but also perform minor maintenance and repairs on the fly.
Improving Efficiency and Reducing Operational Costs
The use of ROVs for visual inspection in deepwater operations offers significant advantages in terms of efficiency and cost-effectiveness.
1. Reduced Downtime
ROVs allow operators to conduct quick, efficient inspections of subsea infrastructure without the need for lengthy and costly human diving operations. With ROVs, visual inspections can be conducted more frequently and at greater depths, enabling early detection of potential issues and reducing the chances of catastrophic failures. This reduces the amount of downtime experienced by subsea operations, saving both time and money.
2. Lower Operational Costs
Traditional human-based inspections often involve complex logistics, including deploying divers, managing dive teams, and coordinating support vessels. In contrast, ROVs are cost-effective alternatives, as they require fewer personnel and can be operated remotely from the surface. Moreover, ROVs can work for extended periods without the need for rest, unlike human divers, resulting in more continuous and cost-effective operations.
3. Enhanced Data Analytics
The real-time data captured by ROVs, including high-definition video feeds and sonar images, can be stored, analyzed, and shared for later review. By using advanced analytics and AI-powered tools, operators can process this data to identify patterns, track changes in infrastructure over time, and predict future maintenance needs. This predictive approach enables proactive maintenance, preventing expensive repairs and extending the lifespan of subsea assets.
The Future of Visual Inspection with ROVs
As ROV technology continues to advance, the future of visual inspections in deepwater operations looks promising. The next-generation ROVs will feature even more sophisticated imaging systems, such as:
- 360-Degree Cameras: These cameras will provide complete panoramic views of subsea structures, eliminating blind spots and ensuring thorough inspections.
- AI-Powered Visual Recognition: Artificial intelligence could enhance ROVs’ ability to recognize and classify defects or abnormalities autonomously, further improving the speed and accuracy of inspections.
- Wireless and Autonomous ROVs: Future ROVs will likely be equipped with wireless capabilities and increased autonomy, allowing them to navigate and inspect areas without the need for a tethered connection to the surface.
Conclusion: Eyes Beneath the Surface
ROVs are truly the robotic eyes beneath the surface, providing enhanced visual inspection capabilities for subsea operations. With high-definition cameras, multispectral imaging, sonar systems, and robotic arms, ROVs offer a level of precision, safety, and efficiency that traditional inspection methods simply cannot match.
As ROV technology continues to evolve, the ability to conduct high-quality, real-time visual inspections in deepwater environments will only improve. This advancement will help industries identify problems early, reduce operational costs, and ensure the continued safety and integrity of underwater infrastructure.
The future of deepwater inspection is clear, and ROVs are leading the way in bringing the ocean’s depths into sharp focus.